Annual Servicing is Key to Avoiding these Forced-Air, Heating/Cooling System Failures
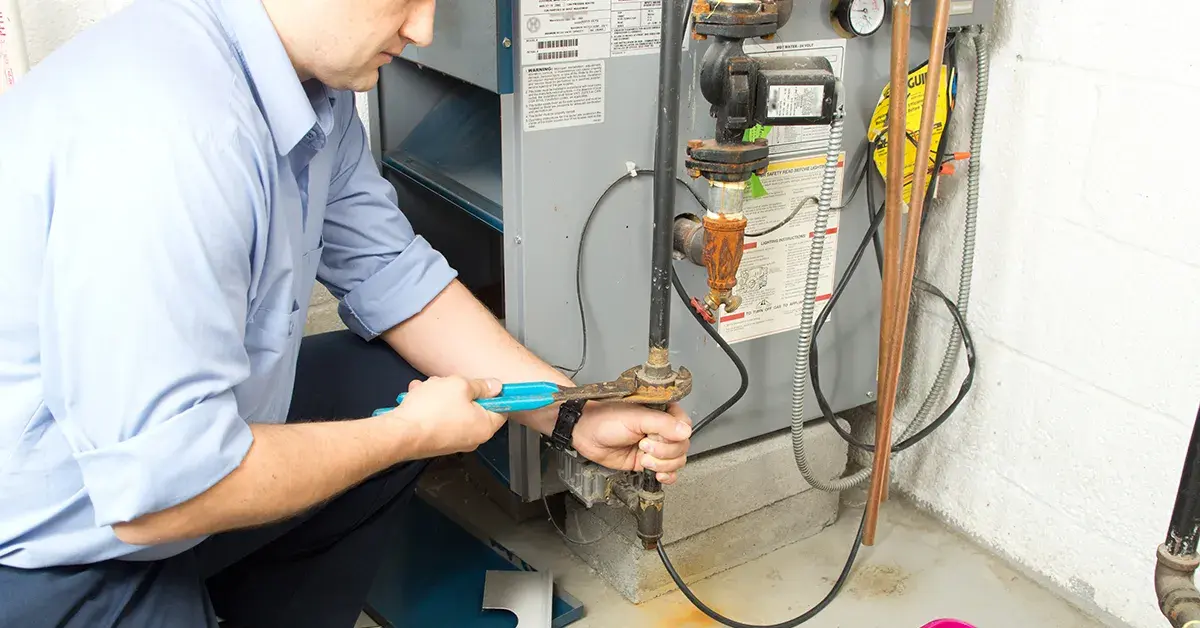
This is the second article in a series about home heating and cooling systems. The first article described the many variations of heating/cooling systems typically found in residential application. After you have identified the heating/cooling system installed in your own home, it is time to make sure you are doing everything possible to maintain the highest safety, efficiency and functionality of your system.
Forced-air heating/cooling systems are one of the most common for residential applications. Most system failures are avoidable with periodic inspection and maintenance by a qualified service provider. We will review the predictable ways these systems can fail when regular maintenance is neglected.
Download the printable guide as a PDF!
Forced-air heating and cooling
This type of system allows a common blower and ductwork to circulate heated and/or cooled air throughout the home. In addition, this air can be easily filtered, humidified, dehumidified, or combined with outside ventilation air as desired. The cooling function of these systems is typically achieved using a refrigerant condensing unit located outside, near the furnace location. Because of the higher complexity of these systems, there is more that can go wrong if maintenance is neglected.
Many ancillary systems such as humidifiers, ventilation dampers, and condensate pumps are a few of the subsystems that can fail and affect the primary system functionality. The ancillary systems may negatively interact with the main system due to electrical interlocks and safety controls used in the overall heating/cooling system.
The heating is typically provided by a natural gas, propane, or fuel oil burner designed into the furnace. Since fuel is burned on-site at the furnace, there are additional safety concerns with proper venting of combustion gases, including carbon monoxide.
A gas-fired burner is a much simpler burner design compared to an oil burner. Each type of burner has a multitude of ways it can fail if maintenance is not performed according to the manufacturer’s recommendations. Some failure modes are common to both types of burners, but others are unique to the fuel used.
Common failure modes for forced- air heating/cooling systems
- Some furnace blower wheels and motors may seize up due to lack of proper bearing lubrication
- Dirty furnace filters can restrict airflow and cause heating and cooling malfunctions or shutdowns
- Plugged condensate pan drains can overflow water on the furnace heat exchanger causing internal cracking or corrosion
- Plugged or defective condensate pumps can trigger safety interlocks that shut down the heating and cooling functions of the furnace
- Belt-driven blowers may have slipping belts or unexpected broken belts causing furnace to malfunction and trip off due to safety control activations
- Furnace may be in an existing or modified location that has insufficient combustion air for the burner to operate safely and properly
- The furnace combustion gas venting to a chimney or through the sidewall PVC vent pipes may have deteriorated or become disconnected due to corrosion or physical damage
- Malfunctioning humidifiers may leak water into ductwork and the furnace causing corrosion or heat exchanger cracking
- Furnace temperate operating controls may fail causing the burner to cycle on the safety control
- Missing blower doors and taped safety switches can cause unsafe and inefficient furnace operation
- The outside condensing unit coils can get plugged with dirt, or grass clippings, causing the air conditioning to malfunction
- Refrigerant leaks can cause the air conditioning system to have reduced cooling or cause coils to ice up
Failure modes unique to gas-fired furnaces
- Improper gas supply pressure to the furnace can cause the burner to have improper combustion and produce excess carbon monoxide
- Natural gas or propane leaks in the piping or control valves may create an explosion hazard in the furnace space
- Pilot lights, where used, may be improperly adjusted for reliable operation
- Burner or heat-exchanger gaskets may fail and cause combustion cases to mix with the blower-circulated house air
- Missing blower doors and taped safety switches can cause unsafe and inefficient furnace operation
Failure modes unique to oil-fired furnaces
- Burner fuel oil nozzle can become plugged causing improper fuel burn rate and oil spray pattern
- Ignition electrodes can become worn or misaligned causing ignition failures
- Dirty or clogged fuel filters and oil pump strainers can reduce the oil flow rate to the burner causing reduced output and improper air-to-fuel mix ratios
- Leaks in the fuel oil supply lines can cause oil to leak out causing oil spills in the furnace area
- Leaks in the fuel oil supply lines can cause air to be sucked into the fuel supply lines, be compressed by the oil pump, and then leak oil into the combustion chamber after the burner is in the off cycle
- Improperly adjusted or dirty air inlets for primary or secondary air damper settings on the burner can cause inefficient burner operation or a dangerous, soot-producing combustion
- Conditions that cause delayed ignition or incomplete shutoff of the fuel supply in the off-cycle can lead to potential for a “puff-back,” or sooty explosion, originating within the combustion chamber and commonly dispersing soot throughout other connected areas of the building
A typical forced-air furnace using gas heat and a cooling coil close-coupled to the top of the furnace
Two condensing units installed outside, but on a wall near the two furnaces in the basement
This article is intended for informational purposes only and does not modify or invalidate any of the provisions, exclusions, terms, or conditions of your insurance policy. Please refer to your policy for actual terms and conditions. All recommendations are general guidelines and are not intended to be exhaustive or complete, nor are they designed to replace information or instructions from the manufacturer of your equipment. Contact your equipment service representative or manufacturer with specific questions.